识别和解决麦克风
Corrosion-resistant alloys (CRA) are used for almost every equipment, machinery, or apparatus used in the食物那乳制品那and饮料制造业。尽管如此,由于这些设备中的腐蚀导致的维护成本令人惊讶地非常高。
Current research in corrosion science and engineering shows that microbes or bacteria have been causing corrosion problems in several other industries as well; from aviation fuels, to oilfields and pipelines, to nuclear waste. In the food, dairy, and beverage manufacturing industries, the same problem exists due to this microbiological issue.
可以通过了解MIC的开发和传播背后的机制来识别植物设备上的微生物诱导腐蚀(MIC)。通过识别MIC,如果未删除,可以最小化其破坏性效果。MIC问题的准确识别和应用预防性维护解决方案可以有效降低整体维护成本。两个独立的植物体验方案,证明如何
场景1:卫生防混阀
乳制品厂的植物经理正在经历卫生混合阀门的问题,这是其中的一部分clean-in-place (CIP)system. This caused disruption in production, contributing to unplanned downtime and product loss.
The company hired CSI to repair all defective valves. Upon thorough inspection of each of the valves, CSI experts found several problems: failed snap rings, broken and leaking air supply lines, and broken actuator springs.
CIS experts were able to determine the specific cause of each of problem, such as incompatible gasket materials, moisture in the air lines causing springs to corrode and fail, and misapplication of heat on the valves (which caused the gaskets to melt and the snap rings to break).
混合阀中的失效垫圈是最重要的问题。失败的垫圈导致食物和CIP流体被困。微生物或细菌开始积聚在阀杆的加工表面上。来自细菌的残留物诱导严重的点蚀和腐蚀,这导致了需要购买或重建零件以更换受损的昂贵的解决方案。
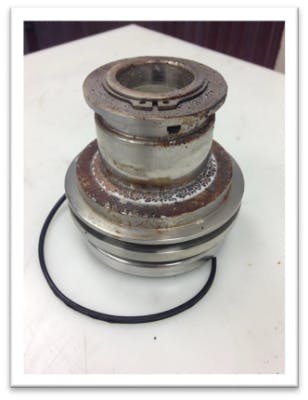
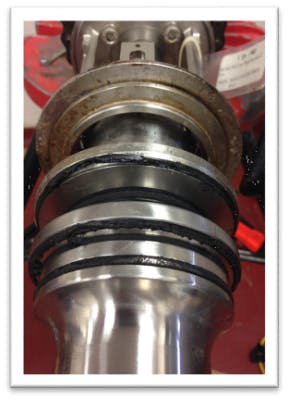
这些照片显示阀门部件和麦克风上的失败垫圈和零件上的蚀。
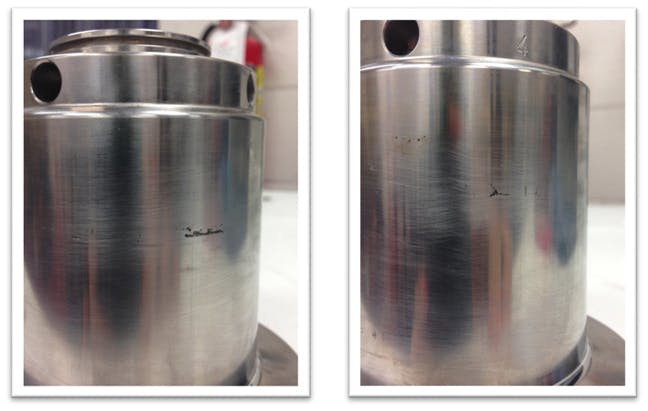
上面的这些照片在阀门部件上显示麦克风和蚀。
Without having a systematic preventive maintenance program, the problems with the gaskets were discovered too late. Their failure, due to incompatibility with the process material, caused food and CIP fluids to enter and become trapped in the areas around the gaskets, which led to the development MIC.
As a result, CSI experts recommended a comprehensive preventive maintenance program, with a focus on a proactive approach against MIC for all sanitary mixproof valves. The maintenance program included the following:
- 改变与工艺材料相容的所有阀门垫片材料。
- 创建预防性维护计划以替换具有与产品兼容的液库。这包括常规时间表进行目视检查,撤销样品阀门,用于彻底内部检查和重大重建。
- 开发清洁图,以帮助质量控制,工程和维护监控特定领域的问题。
- 进行和记录每个阀门的风险评估以及它如何影响产品质量,安全或法律遵从性。
- Testing air supply lines for contamination and cleaning.
- Cleaning the control panel valves and replacement of the defective ones.
- 建立一个替代阀门那计划t are reaching the end of their useful service life.
实施CSI的建议后,客户报告了70,000美元的投资年度返回率为70,000美元。
场景2:CIP返回管道
一个植物维护经理奶酪工厂called CSI to investigate the leaks from corrosion that regularly appeared in the CIP return line. The company sought to understand why a traditionally used corrosion-resistant 304L stainless steel pipe would leak due to corrosion. They had doubts regarding the quality of 304L material and believed the material was possibly not 304L.
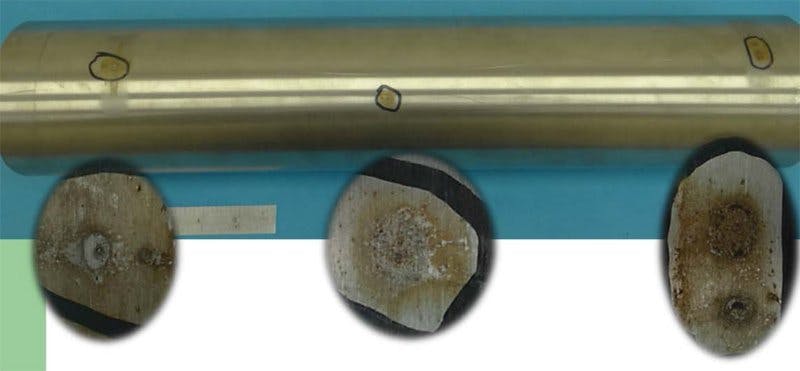
\
This sample shows three areas in the pipe that have through-the-wall leaks.
The client provided a sample piece of the 304L stainless steel tubing, where the leaks were observed. CSI conducted several laboratory tests on the sample to check for material integrity. The tests included photomicrographs, wavelength dispersive X-ray fluorescence (XRF-WD) spectroscopy, optical emission spectroscopy (OES), scanning electron microscopy (SEM), and energy dispersive X-ray spectroscopy (EDS) on the inside and outside surfaces of the sample item.
The results of the spectroscopy tests showed that the elemental composition of the sample conforms to that of a typical 304L stainless steel material. It also revealed unremarkable, but significant, amounts of other elements that appeared to be contaminants and small amounts of phosphorus and chloride, which were most likely from CIP process chemicals.
Consequently, sulfur (S) was found on the pits on the inside surface. Sulfur is believed to be an indication of some sulfate reducing bacteria. The brown material on the inside surface was verified to be iron oxide, or rust.
光谱结果结果在内表面上的凹坑显示出硫的发生,这被认为是硫酸盐还原细菌的指示。

来自金相检查的显微照片表明样品具有304L不锈钢材料的微观结构。此外,它揭示了凹坑的形状与微生物诱导的氯化物蚀均一致。
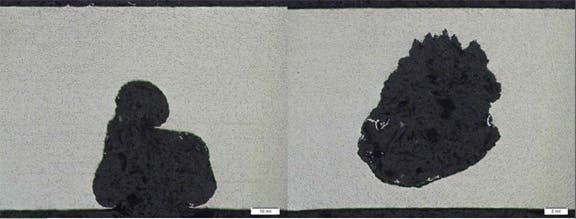
照片显微照片显示了坑的形态。坑广泛而且很大。坑的形状表明坑中的酸性条件。形态与微生物诱导的氯化物点达成一致。
From the laboratory results, CSI experts were able to identify the cause of corrosion on the CIP return pipe as MIC. The bacteria, and resulting corrosion, could be caused by stagnant conditions in the pipes. Had the pipe been operating in full volume, it would have been impossible to form corrosion due to MIC.
CSI was able to prove that the company’s CIP chemicals used, such as the 1% caustic, could not have been the cause of corrosion in the pipes. CSI's findings very strongly indicated the presence of stagnant residual water or residual CIP chemicals at the lower drain regions of the system, which was likely the cause of microbe formation that eventually led to the corrosion. The stagnant conditions provided the environment for bacterial growth, and the residue from the bacteria attacked the metal, causing pits and corrosion.
They reported spending US $96,000 for this problem, in materials alone.
A few of CSI's recommendation based on this experience are:
- Redesigning the process lines to efficiently keep CIP lines drained and dry to avoid stagnant conditions.
- Implement higher corrosion-resistant alloys such asC-22®oral-6xn®。These higher alloys can provide longer life to the process system.
When a comprehensive preventive maintenance program was implemented, the plant’s unexpected downtime was reduced, damage to equipment was minimized, if not eliminated, and the operating life of the systems was extended. Data collected about the equipment being repaired can be utilized for forward planning or for systems upgrades.
Read the article,"Are Microbes Eating Your Sanitary Process System?"to learn more about MIC.
专家BIOS
Yogini Dhopade, Product Specialist - Super Alloys
Yogini Dhopade有三度,讲四种语言,并已经前往世界各地的十个不同国家。她对金属无与伦比的热情,并在CSI中花费时间管理与耐腐蚀合金相关的一切。
Lance Strenfel, Business Development Leader
Lance Strenfel has been a Business Development Leader at Central States Industrial since 2013.
关于CSI.
Central States Industrial Equipment (CSI) is a leader in distribution of hygienic pipe, valves, fittings, pumps, heat exchangers, and MRO supplies for hygienic industrial processors, with four distribution facilities across the U.S. CSI also provides detail design and execution for hygienic process systems in the food, dairy, beverage, pharmaceutical, biotechnology, and personal care industries. Specializing in process piping, system start-ups, and cleaning systems, CSI leverages technology, intellectual property, and industry expertise to deliver solutions to processing problems. More information can be found atwww.xxshagua.com。